6 Sigma Green Belt Certification
Develop the skills required for data-driven process improvement
This certification will help you
- Reduce defects and scrap
- Decrease variation
- Increase process capability
- Improve customer satisfaction
- Use data to improve processes
Members: $1,850 per person
Non-members: $2,850 per person
“From this certification, I gained knowledge of Kaizen events, asking the right questions and working with the operators on their ideas.”
Lillian Brown, Manufacturing Engineer, TT Electronics
“[This is] the best professional class I have ever taken through any training program.”
Adam B, Technical Operations Supervisor
THIS CERTIFICATION INCLUDES
3 EXPERIENTIAL WORKSHOPS + A PROJECT & TEST
(Click the arrows or download a printable flyer to learn more)
Six Sigma Define & Measure
In this workshop, you will learn how to concisely determine goals for an improvement project and communicate them effectively to your peers and leadership.
This workshop will help you solve these problems:
– You don’t know what the customer wants or expects
– You don’t know what the business wants or expects
– You don’t know when your quality is “good enough”
– You don’t develop project charters based on problems relevant to the customer and business
– You don’t have a baseline of your current process performance
Six Sigma Analyze
In this workshop, you will learn how to collect and evaluate data to reduce sources of variation in your process.
This workshop will help you solve these problems:
– You don’ know what is causing performance problems
– You continue to rework the problem and put out fires
– You’re not sure how to quantify the impact of your improvements
– You’re not data literate but you also don’t want to be a statistician
– You’re suffering from analysis paralysis
Six Sigma Improvements & Controls
In this workshop, you will learn how to evaluate sources of variation and apply the data you’ve gathered to make and maintain improvements to your system.
This workshop will help you solve these problems:
– You’re not sure how to select and implement the best solutions
– You’re not sure how to control risk when you test improvement ideas
– You’ve heard about 5-why, fishbone, and cause mapping but don’t know how to use them
– You’ve suffered from backsliding and are not sure how to embed solutions
– Your improvement projects lack closure, they linger and you move on to the next thing
+ Project, Test, & Coaching
Certification Project: All certification applicants are required to demonstrate their ability to apply what they learn by completing a project. This project must include positive measurable results that benefit the company.
Certification Test: All certification applicants are required to complete a test. The test is approximately 15 multiple choice questions and intended to help everyone speak the same language. The test is open book and can be taken multiple times.
Certification Coaching: All certification applicants are required to complete a Learning to Solve Problems coaching session. During coaching you will learn how to be successful from project set-up to completion, mitigate confirmation bias, objectively define problems and apply the Project Template as a project management tool.
Members: $1,850 per person
Non-members: $2,850 per person
Meet a few of our
Experienced Instructors
Susan Weum
Susan Weum is a certified Six Sigma Black Belt, retired from Smiths Medical.
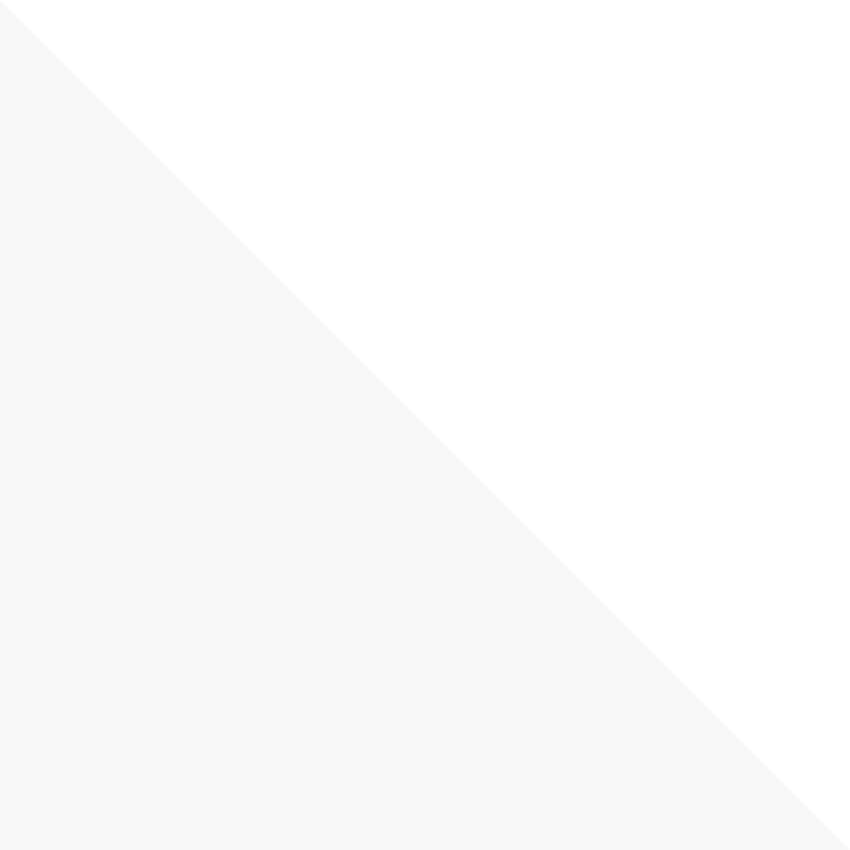
Peter Fritsche
Peter is a Six Sigma Black Belt and has over 25 years of design, operations, and quality leadership experience. During his career, he has supported complex, high technology products manufactured in multiple international facilities in a wide variety of industries.
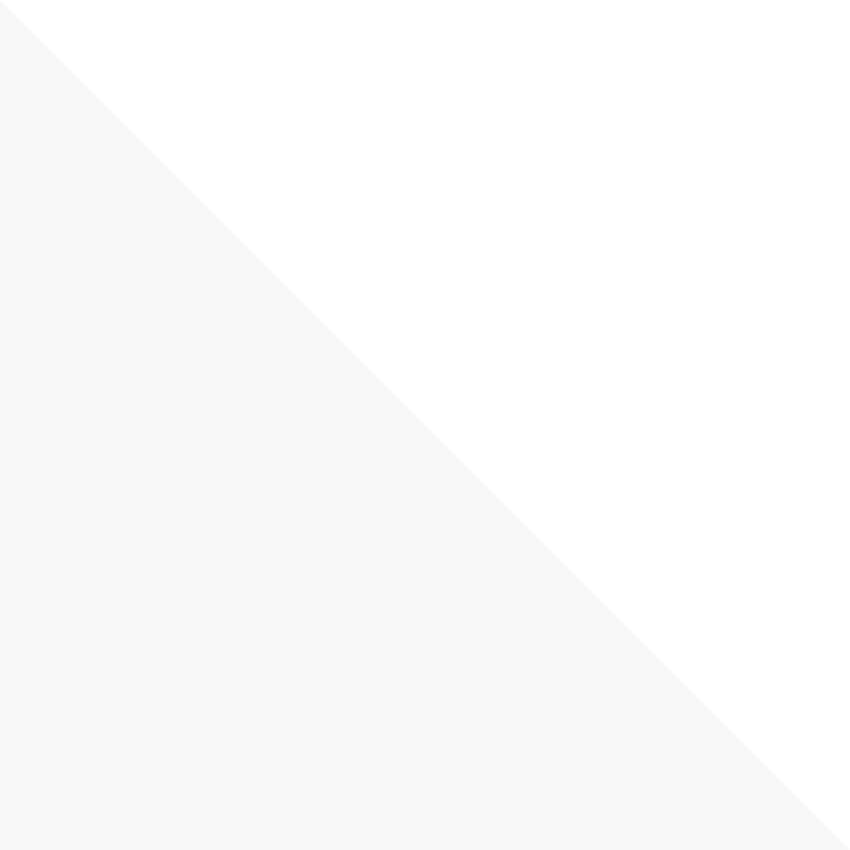
THE PROCESS TO BECOME CERTIFIED
-
Step 1
Enroll in Certification
-
Step 2
Complete training
-
Step 3
Apply what you learn
-
Step 4
Get better results
Want to know about upcoming certification dates?
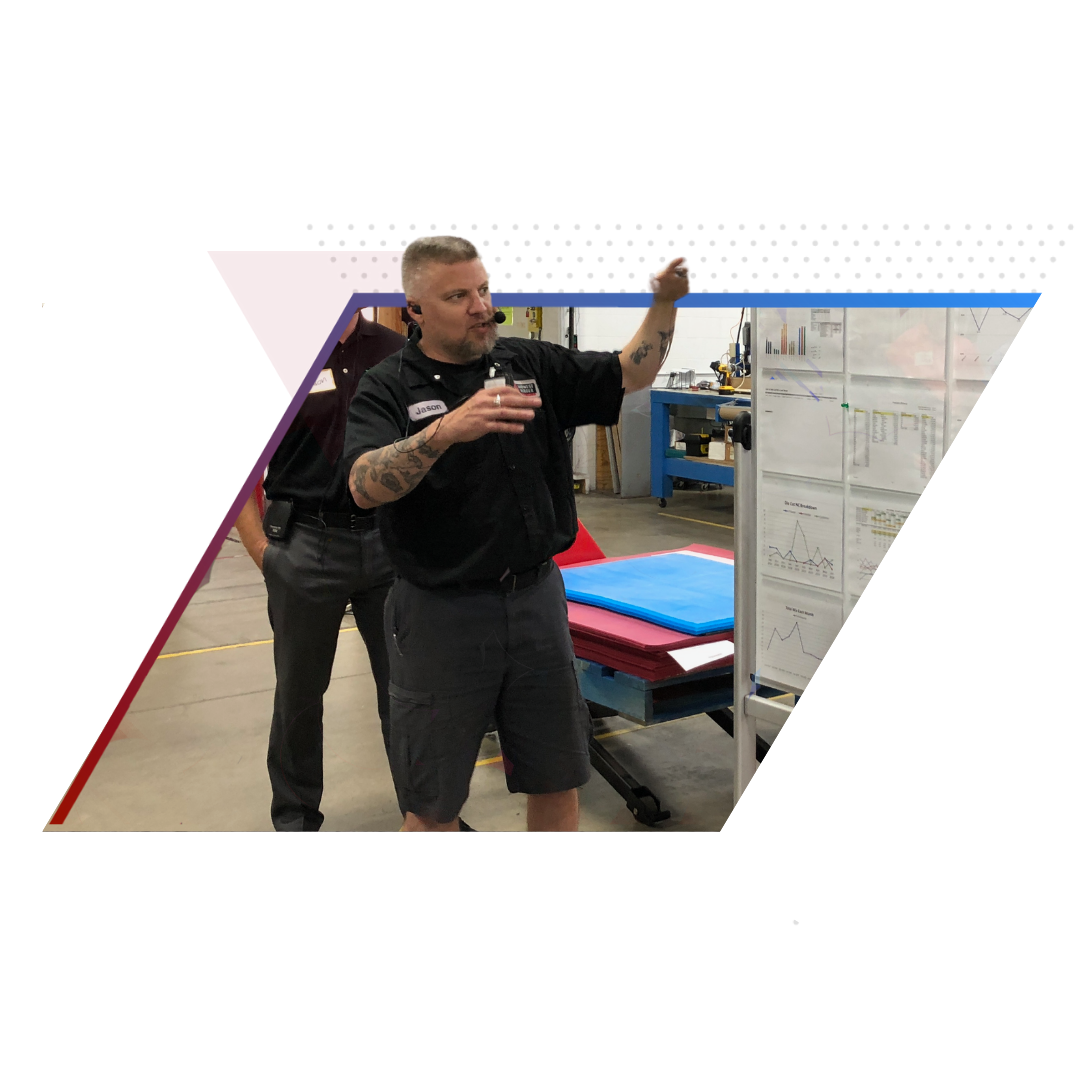
Frequently Asked Questions
What is the time commitment for the certification?
Workshops, project, and final test may be completed in 6-8 months
Who is this certification for?
Quality techs, Engineers, Leads or Supervisors
What types of projects will participants complete?
Click here to view a sample project
Who do I contact to learn more about this certification?
Email our Member Services Manager, Monica at monicas@mfrall.com
Ensure you don’t make these
3 Mistakes Managers Make When Sending People to 6 Sigma Training
It’s easy to get off course and send employees to 6 Sigma Training without proper preparation.
That’s why we’ve created this resource so that you can successfully avoid these pitfalls and see great results!
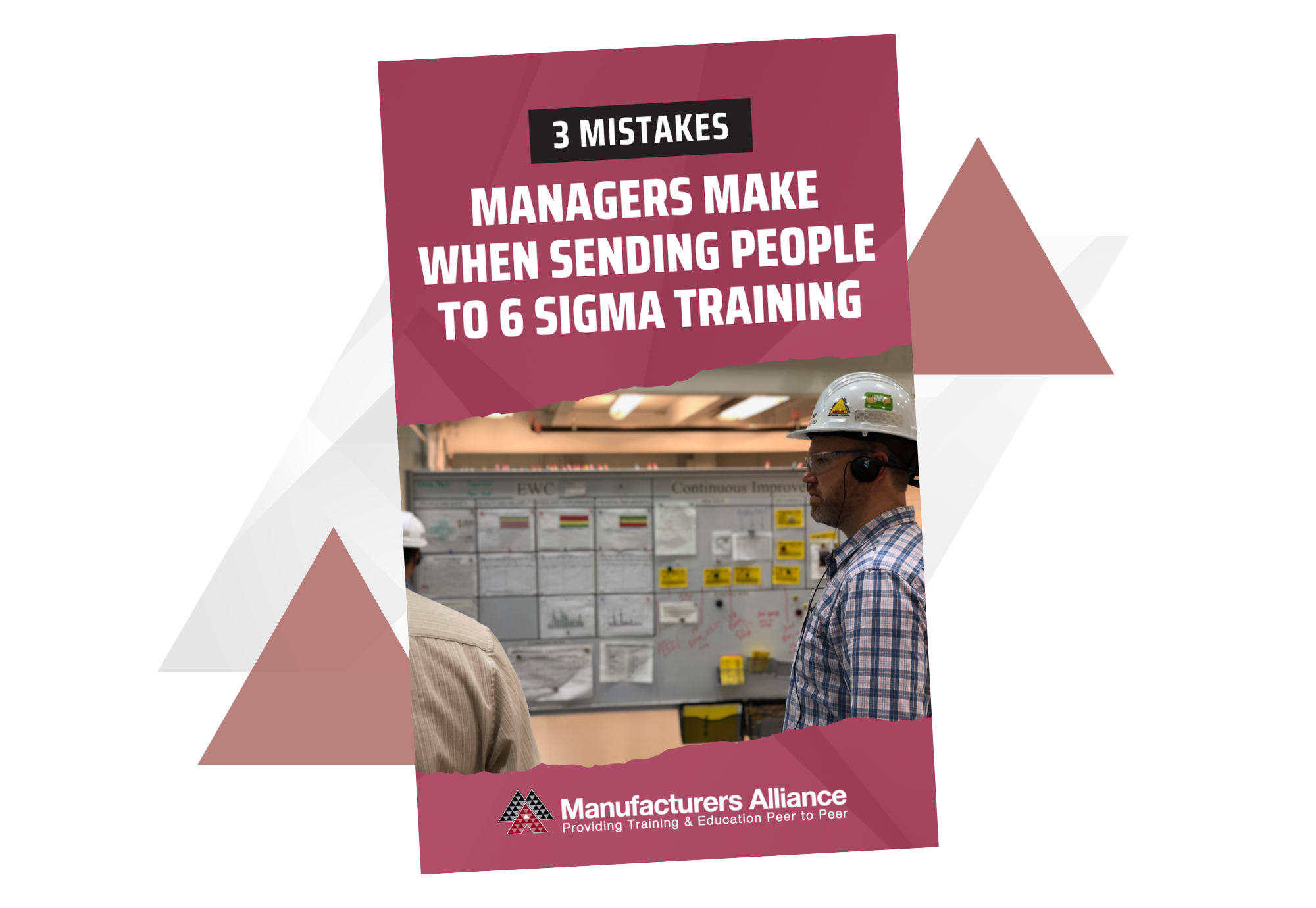