Lean Practitioner Certification
Lean Training Bootcamp at Graco
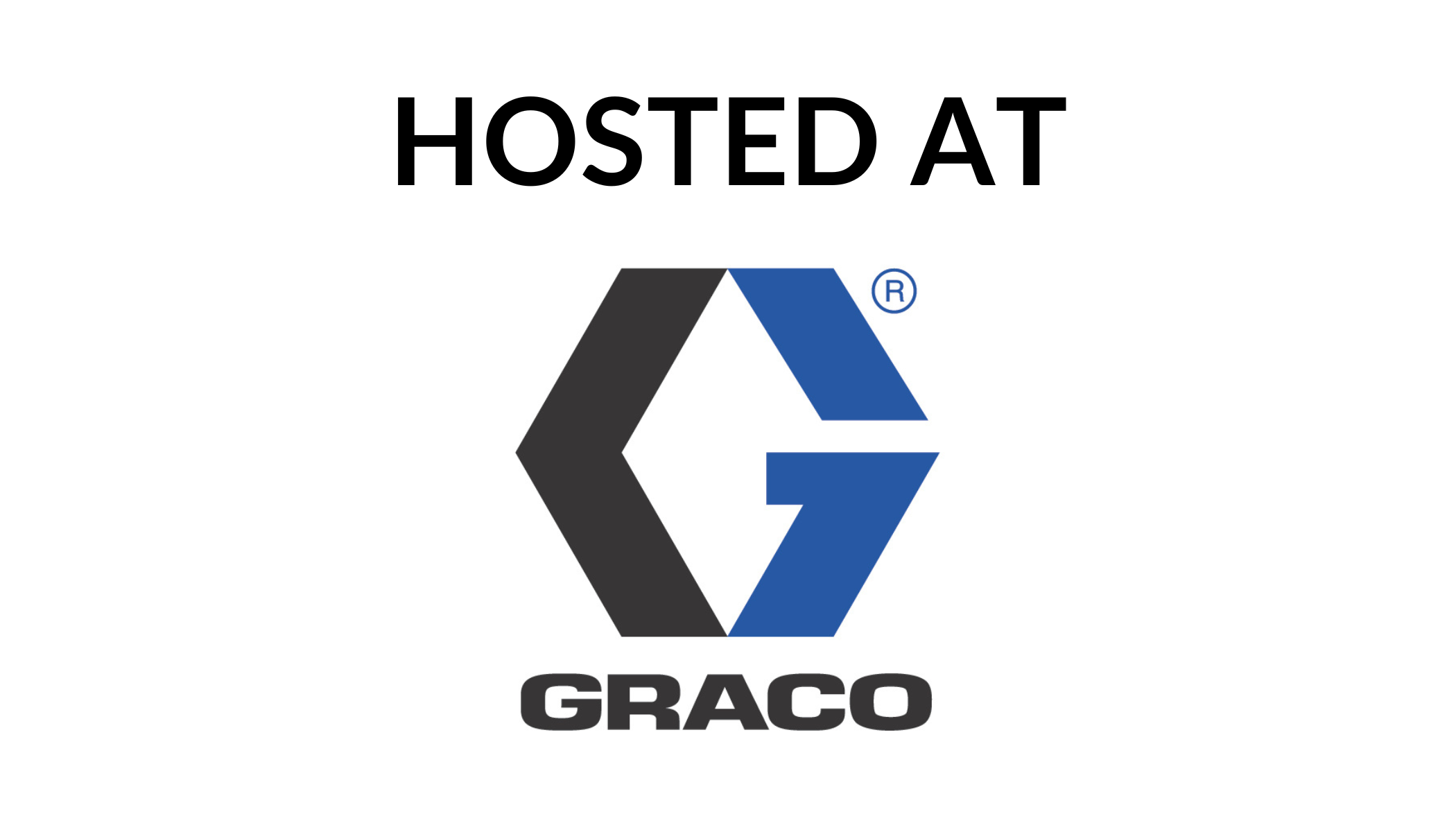
LEARN HOW TO ELIMINATE WASTE & SOLVE PROBLEMS THROUGH:
- Waste Walk on the Floor
- Build a Value Stream Map
- Root Cause Analysis on the Floor
- 5S Scavenger Hunt
- Standard Work at Graco
ENROLLMENT REOPENED – LIMITED SEATS!
Starts April 21, 2025
Members : $2,250
Non-Member: $3,250
THIS CERTIFICATION INCLUDES
6 EXPERIENTIAL WORKSHOPS + A PROJECT, TESTS & COACHING
(Click the arrows to learn more about each)
Learning to see waste Simulation – April 22nd Morning
Would you like to experience the benefits of Lean manufacturing? For many, the first step in creating a culture of continuous improvement and developing an army of problem solvers is to help all employees identify opportunities for improvement. Participants gain knowledge and the tools required in order to help a critical mass of employees learn how to define value and identify and eliminate waste. After completing the workshop, participants will have experienced the difference between traditional and Lean manufacturing and its components.
Tools and Topics Learned Include:
• The common forms of waste
• Practical brainstorming techniques
• Kanban
• Visual Controls
• Kaizen Events
• Teamwork
• Value Stream Mapping
• Cellular manufacturing
• Work Standardization
Creating Process Maps – April 22nd Afternoon
Mapping demonstrates how Lean thinking can reduce process timelines and improve quality and delivery to schedule. In this session, participants will map out real processes and learn about pre and post mapping tools to add to their personal toolbox. Participants will learn a simple 3-step process for change management and leave with an entire cache of tools to assist through successful process improvement deployment and sustainment.
Tools and Topics Learned Include:
• Lean Principles for Mapping
• Prework for Successful Mapping Sessions
• Swim Lane Mapping, Value Stream, Spaghetti, Ideal State, and Future State Maps
• Post Mapping Tools
• The People Side of Change Management-3 Step Process
Root Cause Analysis – April 23rd Morning
Does the desire to act overpower the need to understand? Understanding the problem, the process, the people and the distinctions between the types of causes are all stepping stones to effective root cause analysis to permanently eliminate problems from recurring. When structured methods and tools are used, this can be accomplished.
Tools and Topics Learned Include:
• RCA Principles and Process Steps
• Importance of Group Dynamics and having the RIGHT team
• Tools to assist in thoroughly defining the Problem Statement
• RCA tools for identifying symptoms, contributing causes and root causes
• Why the 5 Why Technique isn’t always enough
• Importance of performing data collection and validation
Visual Management and 5S – April 23rd Afternoon
Customers, employees and suppliers can tell a well-run plant and office without a narrated tour. The visual clues are everywhere. This is a straightforward approach that impacts your customer and employee image, productivity and sales. The many facets of visual management and 5S can allow employees to show pride and organization in their area, give them performance feedback, provide incentive to hit their goals, illustrate what is expected of them and recognize a job well done. These techniques can help overcome language and reading barriers and boost learning retention too.
Tools and Topics Learned Include:
• Visual display boards
• Standard work boards
• Visual control boards
• Color-coding time savers
• Motivating teams for higher performance
• Pictorial procedures
• Visual performance measurements
• 5S organizing and housekeeping
Standard Work – April 24th Morning
“Without Standard Work, there can be no improvement.” This statement is a central truth of the Toyota Production System. Standard work defines the current best work process. It is the baseline for continuous improvement and is a tool used in auditing processes. Therefore, conformance to standard work contributes to the results you need to stay competitive but is something we really don’t want to do. Until you can apply repeatable standard work successfully, improvements will yield less than their full potential and backsliding will be prevalent. Participants will walk away with the knowledge, tools, and confidence they need to be able to begin to apply Standard Work in their operations on the very next day.
Tools and Topics Learned Include:
• Time and motion study techniques
• Work cell and assembly line loading
• Details of standardized work documents
• Developing a process to sustain standardized work
Kaizen Rapid Improvement – April 24th Afternoon
Do you need productivity and cost improvements now? This workshop will provide the education and experience that is necessary for you to deploy rapid improvement teams at work. Participants will learn to measure what is important, gather the necessary resources, decide who does what, and set and accomplish a one week schedule for project completion. Most importantly, you will see how to accomplish more in less time than most teams take to agree on what they should be doing. Attendees participate in interactive team exercises that demonstrate in a practical manner the application of rapid improvement principles and techniques.
Tools and Topics Learned Include:
• Rapid improvement process tools
• Performance measurement tools
• Simulation of a rapid improvement project
• How to overcome barriers
+ A Project, Tests, & Coaching
Certification Project: All certification applicants are required to demonstrate their ability to apply what they learn by completing a project. This project must include measurable results that benefit the company.
Certification Tests: All certification applicants are required to complete a test after each workshop. Each test is approximately 15 multiple choice questions and intended to help everyone speak the same language. Tests are open book and can be taken multiple times.
Certification Coaching: All certification applicants are required to complete a Learning to Solve Problems coaching session help on November 12th (1-3PM) over Zoom. During coaching you will learn how to be successful from project set-up to completion, recognize and mitigate bias, objectively define problems, learn where, how and when to access resources, and apply the Project Template as a project management tool.
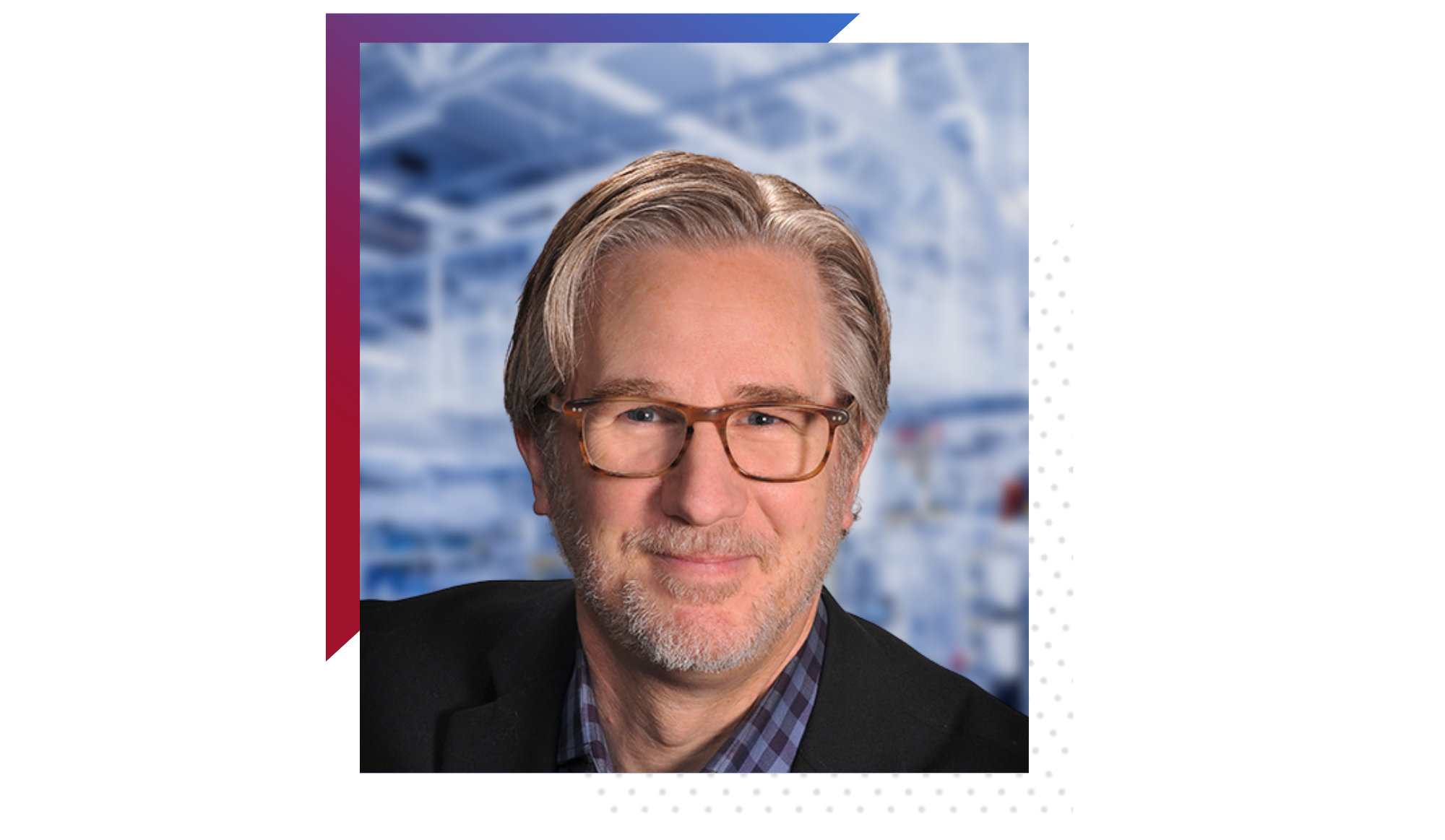
Your Instructor
Michael Muilenburg is an instructor and Peer Group Facilitator with the Manufacturers Alliance. During his 36-year career at 3M he worked in manufacturing operations, process development, product development, Lean Six Sigma and supply chain. Michael most recently served as the Operations Technology Director for 3M’s Film and Material Resource Division.
ENROLLMENT REOPENED – LIMITED SEATS!
Starts April 21, 2025
Members : $2,250
Non-Member: $3,250
Fast-track the lean practitioner training you know and trust
Send Your Out of town employees
Directions
How to get to the bootcamp headquarters
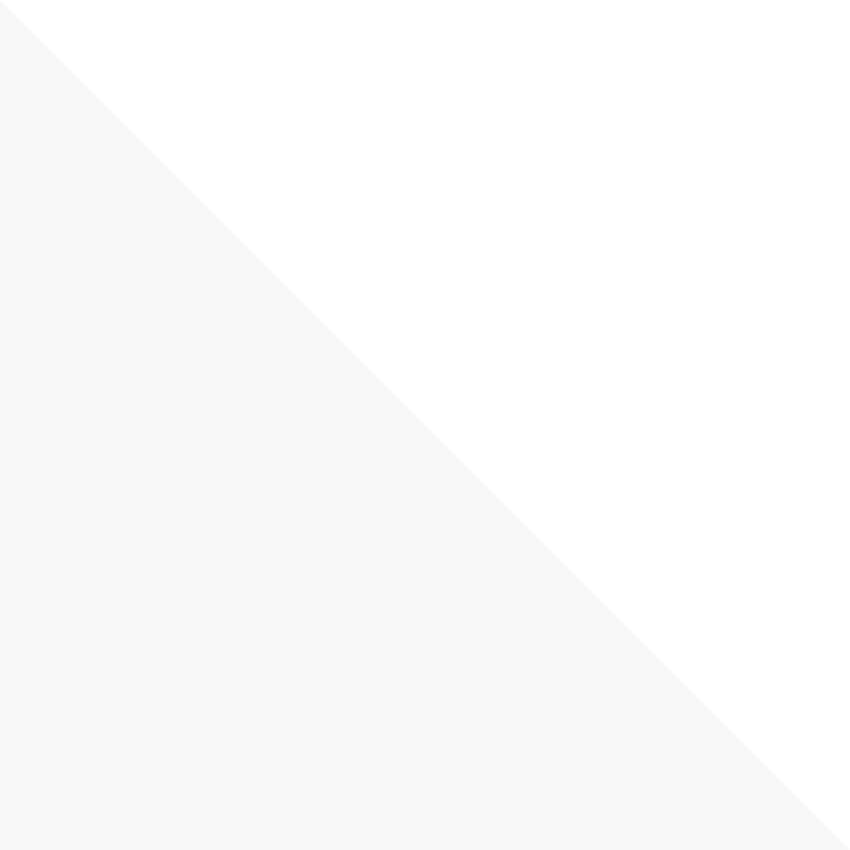
Hotels
Our curated reccomendations for hotels near Graco, Rogers.
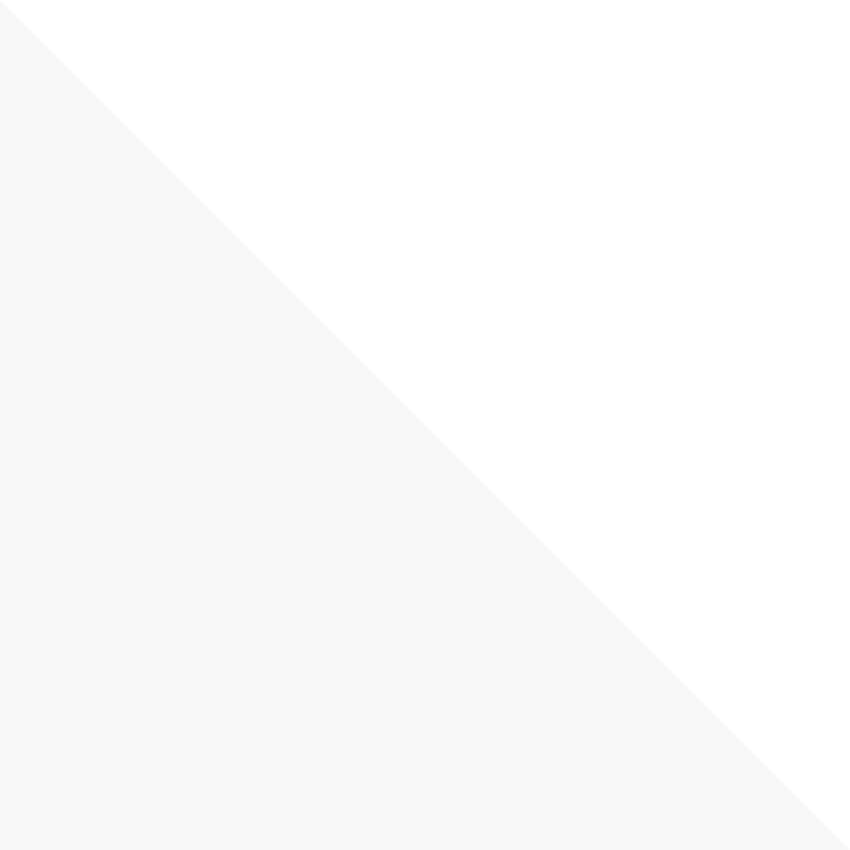
Restaurants
Our top restaurant picks near the bootcamp training site
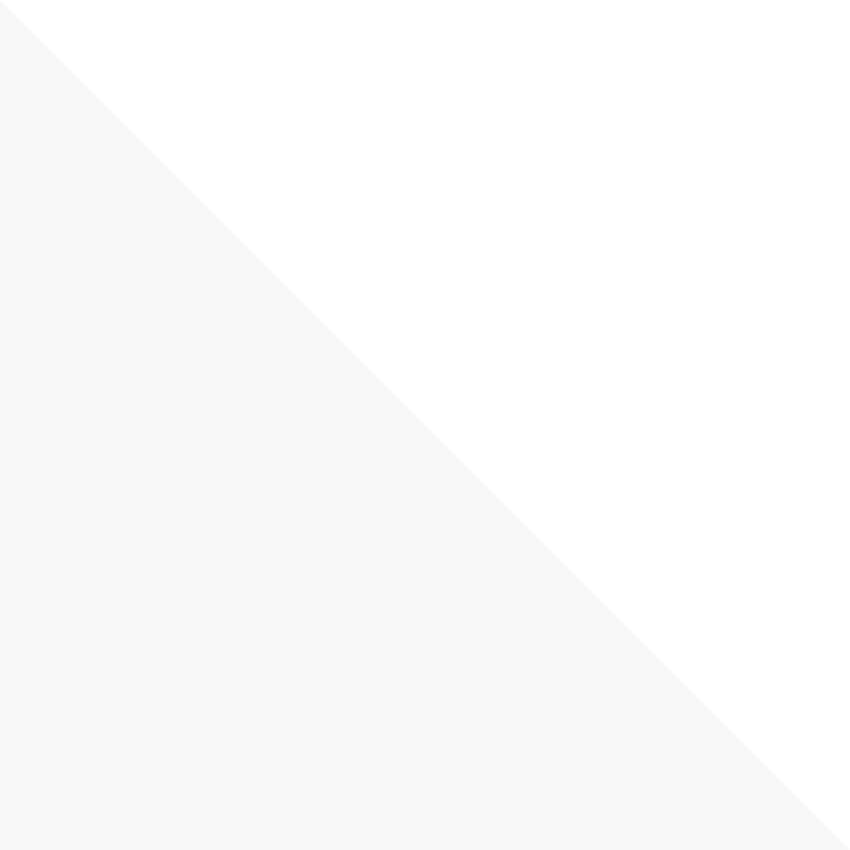
“My biggest problem was not having practical knowledge of lean tools. I’ve applied today’s learnings by identifying waste more intentionally on the shop floor and including shop employees in the entire process.”
Sam Martin, Continuous Improvement Specialist
“My biggest problem was not getting buy-in. Now I know how to ask the right questions and listen. I’ve applied the learnings by not beginning with the solution in mind, but by getting the facts using a scientific approach.”
Page Townsend, CI Leader
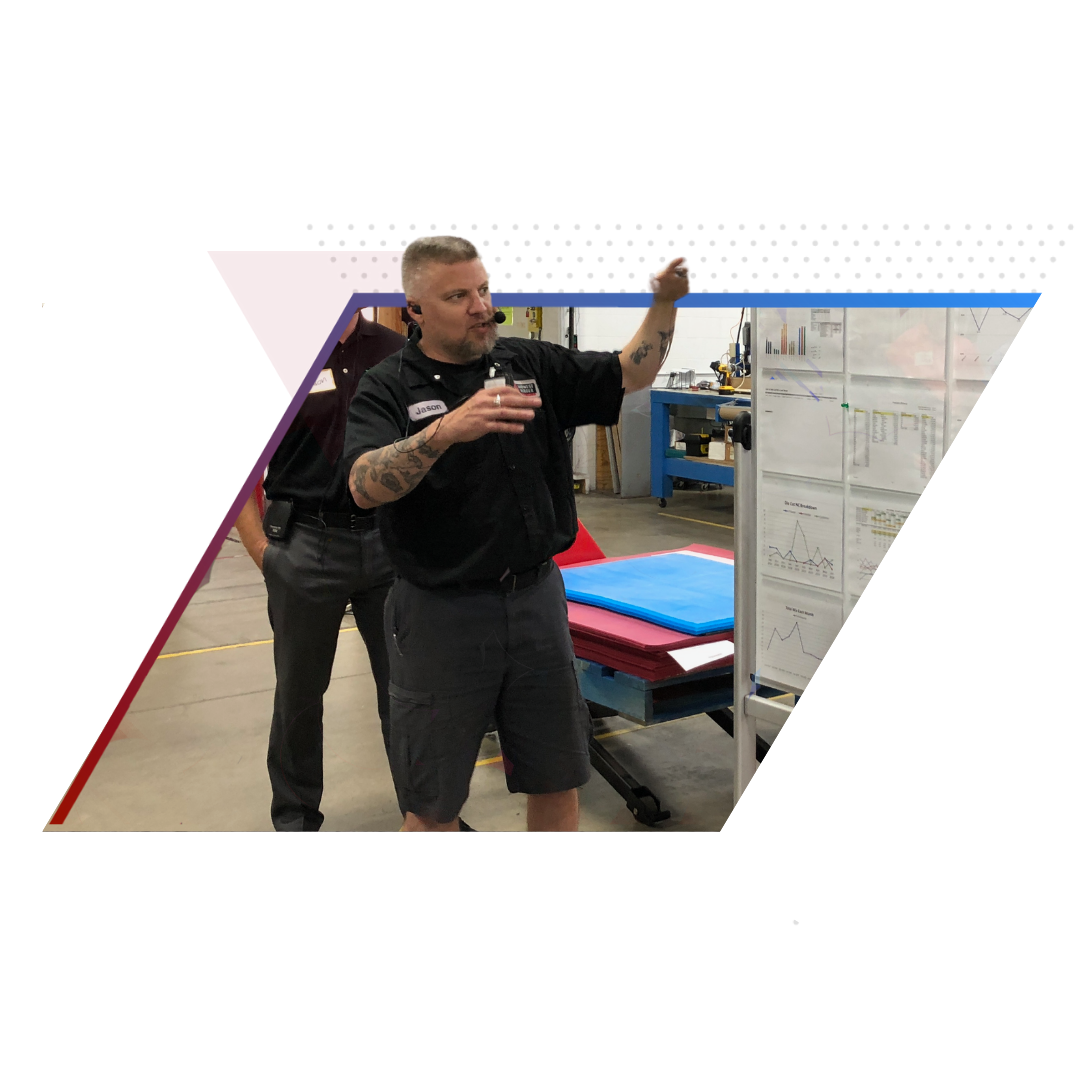
Frequently Asked Questions
Who is this certification for?
Mfg, Industrial, and Quality Engineers, and Department Leads or Supervisors
What is the time commitment?
This certification is a half-day bootcamp spanning six consecutive business days from November 13th-22nd from 8:00am-12:00pm. The Learning to Solve Problems coaching session is November 12th from 1:00pm-3:00pm. Workshops, tests, and project work may be completed in 6-12 months
Where is the training hosted?
This certification is hosted at Graco in Rogers, MN.
What type of project will participants complete?
Click here to view a real-world project
THE PROCESS TO BECOME CERTIFIED
-
Step 1
Enroll in Certification
-
Step 2
Complete Bootcamp
-
Step 3
Apply what you learn
-
Step 4
Get better results
ENROLLMENT REOPENED – LIMITED SEATS!
Starts April 21, 2025
Members : $2,250
Non-Member: $3,250